Optimisation de la Qualité de l’Air dans le Traitement de Surface Industriel
Introduction
Le traitement de surface est un ensemble de procédés qui modifie les propriétés physiques ou chimiques d’une pièce pour la rendre plus résistante, la protéger contre la corrosion ou encore améliorer son aspect visuel. Ce secteur inclut une large variété d’industries, de l’aéronautique à l’automobile, en passant par la métallurgie et l’électronique. Toutefois, ces procédés génèrent des émissions de polluants atmosphériques, souvent sous forme de poussières métalliques, brouillards d’huile ou vapeurs de solvants, représentant un risque pour la santé des opérateurs et l’environnement. ISPIRA, spécialiste de la qualité de l’air industriel et membre de l’UITS (Union des Industries des Technologies de Surface), accompagne les entreprises dans l’évaluation des Valeurs Limites d’Exposition Professionnelle (VLEP) et la gestion des rejets atmosphériques des ICPE (Installations Classées pour la Protection de l’Environnement) dans ce secteur.
Figure 1 – Boules en acier inoxydable avec traitement de surface optimisé – Ces boules en acier inoxydable poli sont le résultat d’un traitement de surface spécifique, incluant un procédé de polissage à billes. Ce traitement confère aux boules une résistance accrue à l’eau et aux intempéries, garantissant leur durabilité dans des environnements extérieurs. Le processus est conforme aux meilleures pratiques de protection des surfaces métalliques contre la corrosion et l’usure, dans le respect des normes de qualité de l’air et des rejets atmosphériques pour les installations industrielles.
Cas d’Application
Dans ce cadre, ISPIRA a collaboré avec plusieurs industries du traitement de surface, confrontées à des problématiques similaires mais variées en fonction des procédés utilisés. Voici trois exemples concrets.
1. Atelier d’anodisation de pièces pour l’aéronautique
L’anodisation, procédé électrochimique clé dans l’aéronautique, améliore la résistance à la corrosion des pièces en aluminium en créant une couche d’oxyde d’aluminium. Cette protection renforce la durabilité des pièces face aux intempéries et agents chimiques, rendant ce traitement indispensable dans les industries où la performance des matériaux est cruciale.
Description du Procédé
L’anodisation se déroule en plusieurs étapes : un dégraissage suivi d’un décapage pour nettoyer les surfaces. Ensuite, les pièces sont plongées dans un bain d’acide sulfurique où un courant électrique forme la couche d’oxyde. Enfin, elles sont rincées et parfois colorées pour accroître leur résistance. Ces étapes s’effectuent dans des cuves de bains chimiques, générant des émissions de polluants.
Risques liés aux Émissions Atmosphériques
Les bains acides, notamment à base d’acide sulfurique, produisent des brouillards acides nocifs pour la qualité de l’air dans l’atelier. Ces brouillards peuvent irriter les voies respiratoires des opérateurs et endommager les installations si les vapeurs ne sont pas correctement captées. Ces émissions représentent un risque majeur pour la santé si elles dépassent les Valeurs Limites d’Exposition Professionnelle (VLEP).
Pour limiter les risques, il est crucial de mettre en place des systèmes de captation à la source et de ventilation efficaces, capables d’aspirer les brouillards acides dès leur formation. Ces dispositifs garantissent une meilleure qualité de l’air et protègent les opérateurs de toute exposition prolongée.
Solutions mises en place par ISPIRA :
- Audit de la ventilation et dimensionnement des systèmes de captation à la source avec aspiration latérale sur les cuves de traitement de surface, avec des vitesses de captage conformes aux recommandations de l’INRS (ED 6523).
- Etude technico-économique pour le dimensionnement et la mise en œuvre de colonnes de lavage physico-chimique des effluents gazeux avant leur rejet à l’atmosphère.
- Mesures et contrôles périodiques des concentrations en acides, cyanures, chrome hexavalent dans l’air ambiant des ateliers et sur les opérateurs, garantissant des niveaux inférieurs aux Valeurs Limites d’Exposition Professionnelle (VLEP).
- Accompagnement à la réponse à l’Inspection du Travail et à la DREAL sur l’ensemble des actions d’amélioration mises en œuvre : audit et mise à niveau de la ventilation, dimensionnement et installation des laveurs de gaz physico-chimiques, contrôles périodiques des VLEP.
Figure 2 – Système de captation bilatérale des effluents gazeux dans un atelier de traitement de surface – Captation des émissions de métaux lourds et d’acides pour améliorer la qualité de l’air et prévenir l’exposition des opérateurs aux agents chimiques.
2. Atelier de revêtements par électrodéposition
L’électrodéposition est un procédé utilisé pour recouvrir des pièces métalliques avec une fine couche de métal, afin de les protéger contre la corrosion ou d’améliorer leur aspect esthétique. Ce processus fait appel à des bains de solutions métalliques et à un courant électrique qui permet de déposer les ions métalliques sur la pièce immergée. Les métaux les plus fréquemment utilisés pour ce procédé incluent le cuivre, le nickel, le chrome et le zinc.
Description du Procédé
Les principales étapes de ce procédé comprennent :
- Le nettoyage des pièces : Dégraissage et décapage chimique pour éliminer les impuretés.
- L’électrodéposition : Les pièces sont plongées dans des bains contenant des sels métalliques dissous, sous l’action d’un courant électrique, pour obtenir le revêtement souhaité.
- Le rinçage : Ce procédé permet d’éliminer les résidus chimiques avant et après le traitement.
Risques liés aux Émissions Atmosphériques
Les procédés d’électrodéposition émettent divers contaminants atmosphériques dangereux, tels que des acides, des métaux lourds, et parfois des cyanures. Ces contaminants peuvent se propager dans l’air sous forme de brouillards acides, d’aérosols métalliques ou de gaz toxiques comme l’acide cyanhydrique. Ces émissions posent un risque sérieux pour la santé des opérateurs, notamment en termes de troubles respiratoires et cutanés.
Les principales substances concernées sont :
- Chrome hexavalent (Cr(VI)) : Utilisé pour le chromage, il est extrêmement toxique et classé dans la catégorie 1 (1A) des cancérogènes par l’Union européenne.
- Nickel et cuivre : Métaux fréquemment utilisés, se retrouvant dans les effluents atmosphériques et dans les particules fines.
- Acides sulfurique et nitrique : Génèrent des brouillards acides susceptibles d’irriter les voies respiratoires et d’endommager les équipements.
Solutions mises en place par ISPIRA :
- Audit de la ventilation, dimensionnement et optimisation de la ventilation générale et des systèmes de captation à la source, avec système d’aspiration à fentes placé autour des cuves d’acide, pour assurer un renouvellement constant de l’air dans les zones critiques. Mise en conformité des vitesses de captage avec les recommandations de l’INRS (ED 6523).
- Audit de fonctionnement et remise en conformité des laveurs physico-chimiques des effluents gazeux avant leur rejet à l’atmosphère (tour de lavage cyanure et tour de lavage acido-basique).
- Mise en place d’un programme de mesures régulières de la qualité de l’air et de contrôles périodiques des concentrations en acide, sulfurique et nitrique, cyanures, chrome hexavalent et métaux dans l’air ambiant des ateliers et sur les opérateurs, garantissant des niveaux inférieurs aux Valeurs Limites d’Exposition Professionnelle (VLEP).
- Accompagnement pour la réponse à l’Inspection du Travail et à la DREAL : audit et mise à niveau des systèmes de ventilation, dimensionnement et implémentation des laveurs de gaz physico-chimiques, ainsi que mise en place d’un programme de contrôles périodiques des VLEP pour garantir la conformité et la sécurité des installations industrielles.
Figure 3 – Système de captation des effluents gazeux dans un atelier de traitement de surface, avec des vitesses de captage conformes aux recommandations de l’INRS – Captation des émissions de métaux lourds et d’acides pour améliorer la qualité de l’air et prévenir l’exposition des opérateurs aux agents chimiques.
3. Atelier de galvanisation à chaud
La galvanisation à chaud est un procédé essentiel pour la protection des pièces métalliques contre la corrosion. Cette technique consiste à plonger les pièces dans un bain de zinc en fusion à environ 450°C, ce qui permet de former un revêtement protecteur. Ce revêtement offre une résistance exceptionnelle aux intempéries, à l’eau et aux produits chimiques, ce qui prolonge considérablement la durée de vie des structures métalliques dans des environnements difficiles.
Description du Procédé
Les étapes principales de la galvanisation à chaud comprennent :
- Préparation des pièces : Nettoyage préalable des pièces à galvaniser à l’aide de bains de dégraissage, de décapage acide, et de rinçage pour éliminer les impuretés.
- Fluxage : Un bain de flux est appliqué pour favoriser l’adhésion du zinc à la surface métallique.
- Trempage dans le bain de zinc : La pièce est plongée dans un bain de zinc en fusion, formant une couche protectrice par réaction chimique entre le zinc et l’acier.
- Refroidissement : Les pièces sont ensuite refroidies dans l’air ou dans un bain d’eau, permettant de fixer le revêtement de zinc.
Risques liés aux Émissions Atmosphériques
La galvanisation à chaud produit plusieurs types d’émissions atmosphériques potentiellement nocives. Ces émissions proviennent principalement des bains de zinc en fusion et des réactions chimiques qui s’y produisent, incluant des vapeurs de zinc, des oxydes métalliques, ainsi que des poussières lors des opérations d’écrémage.
Les principales substances émises incluent :
- Oxydes de zinc : Émis sous forme de particules fines, ces oxydes peuvent causer des troubles respiratoires chez les opérateurs.
- Acide chlorhydrique : Utilisé dans les bains de décapage, il génère des brouillards acides nécessitant une captation adéquate pour protéger les opérateurs.
- Particules métalliques : Provoquées par les processus d’écrémage et de manipulation des pièces galvanisées, elles peuvent se disperser dans l’air.
Ces émissions présentent des risques importants pour la santé des opérateurs, notamment en termes d’inhalation de poussières de zinc et de vapeurs acides.
Solutions mises en place par ISPIRA :
Dans le cadre de l’accompagnement des ateliers de galvanisation à chaud, ISPIRA a mis en œuvre des solutions adaptées pour optimiser la qualité de l’air et garantir la conformité aux normes réglementaires. Voici les principales actions réalisées :
- Audit de la ventilation : ISPIRA a réalisé une évaluation complète des systèmes de ventilation existants, permettant d’identifier les zones critiques et de recommander des optimisations pour améliorer la circulation de l’air et réduire les émissions de vapeurs de zinc.
- Amélioration de l’encapsulation du bain de zinc : pour limiter la propagation des fumées de zinc, ISPIRA a conseillé l’amélioration des systèmes d’encapsulation des bains, associés à une extraction d’air performante pour prévenir l’exposition des opérateurs.
- Contrôle des VLEP : mise en place d’une stratégie et d’un programme de mesures régulières avec un organisme accrédité COFRAC pour surveiller les niveaux de particules métalliques et d’oxydes de zinc dans l’air ambiant, garantissant que les concentrations respectent les Valeurs Limites d’Exposition Professionnelle (VLEP).
- Accompagnement technique pour la conformité : ISPIRA a assisté les entreprises dans la préparation des réponses à l’Inspection du Travail et à la DREAL, en mettant l’accent sur les actions correctives concernant la ventilation industrielle et la gestion des rejets atmosphériques.
Ces solutions ont permis de renforcer la sécurité des opérateurs et d’assurer un environnement de travail conforme aux exigences en matière de qualité de l’air.
Figure 4 – Bain de zinc dans un atelier de galvanisation à chaud, avec système de captation des vapeurs – Système performant de captation des vapeurs de zinc (encapsulation du bain de zinc avec extraction d’air) pour prévenir l’exposition des opérateurs aux agents chimiques et améliorer la qualité de l’air dans les ateliers de galvanisation à chaud.
Résultats et Bénéfices
Grâce à l’accompagnement spécialisé d’ISPIRA dans les ateliers de traitement de surface, incluant l’anodisation, les revêtements par électrodéposition et la galvanisation à chaud, les industriels ont observé des résultats significatifs en matière de qualité de l’air et de conformité réglementaire.
- Réduction des émissions atmosphériques : Grâce aux audits et aux recommandations d’ISPIRA, les industriels ont pu mettre en place des systèmes de captation et de traitement d’air adaptés à leurs besoins spécifiques. Cela a permis de limiter efficacement les émissions de brouillards acides, de métaux lourds, et d’autres substances dangereuses. Ces actions ont amélioré la qualité de l’air dans les ateliers, protégeant ainsi la santé des opérateurs.
- Respect des VLEP : ISPIRA a effectué des mesures régulières et des contrôles des Valeurs Limites d’Exposition Professionnelle (VLEP) pour les substances dangereuses telles que le chrome hexavalent, le nickel ou les oxydes de zinc. Les recommandations apportées ont permis aux entreprises de se conformer pleinement aux exigences réglementaires en matière de sécurité des travailleurs, en réduisant les risques d’exposition à des substances nocives.
- Optimisation de la ventilation : Les audits aérauliques menés par ISPIRA ont permis d’optimiser les systèmes de ventilation industrielle. En accompagnant les entreprises dans le dimensionnement et la mise en œuvre de solutions adaptées, ISPIRA a contribué à améliorer le renouvellement de l’air dans les ateliers et à réduire les concentrations de polluants. Ces optimisations ont favorisé un environnement de travail plus sain et plus productif.
- Réduction de l’impact environnemental : En accompagnant les industriels dans la gestion de leurs rejets atmosphériques, ISPIRA a aidé ses clients à se conformer aux réglementations relatives aux Installations Classées pour la Protection de l’Environnement (ICPE). En réduisant les émissions de substances nocives, les entreprises ont pu améliorer leur empreinte environnementale tout en renforçant leur engagement envers la durabilité et la sécurité.
En résumé, l’accompagnement d’ISPIRA a permis aux industriels d’améliorer durablement la qualité de l’air dans leurs ateliers, de respecter les normes de sécurité et environnementales, tout en garantissant une meilleure performance des installations et des conditions de travail optimales pour les opérateurs.
Si vous souhaitez optimiser la qualité de l’air dans vos ateliers de traitement de surface, améliorer la sécurité de vos opérateurs et garantir la conformité aux normes environnementales et de sécurité, ISPIRA est votre partenaire expert. En tant que bureau d’étude spécialisé, nous réalisons des audits, des mesures de qualité de l’air et des évaluations des VLEP, tout en vous accompagnant pour le dimensionnement et la mise en œuvre des solutions les mieux adaptées à vos installations.
Contactez nos experts pour bénéficier de notre expertise et améliorer durablement vos performances en matière de gestion de l’air industriel. Découvrez nos services sur notre page dédiée à la mécanique et au traitement de surface.
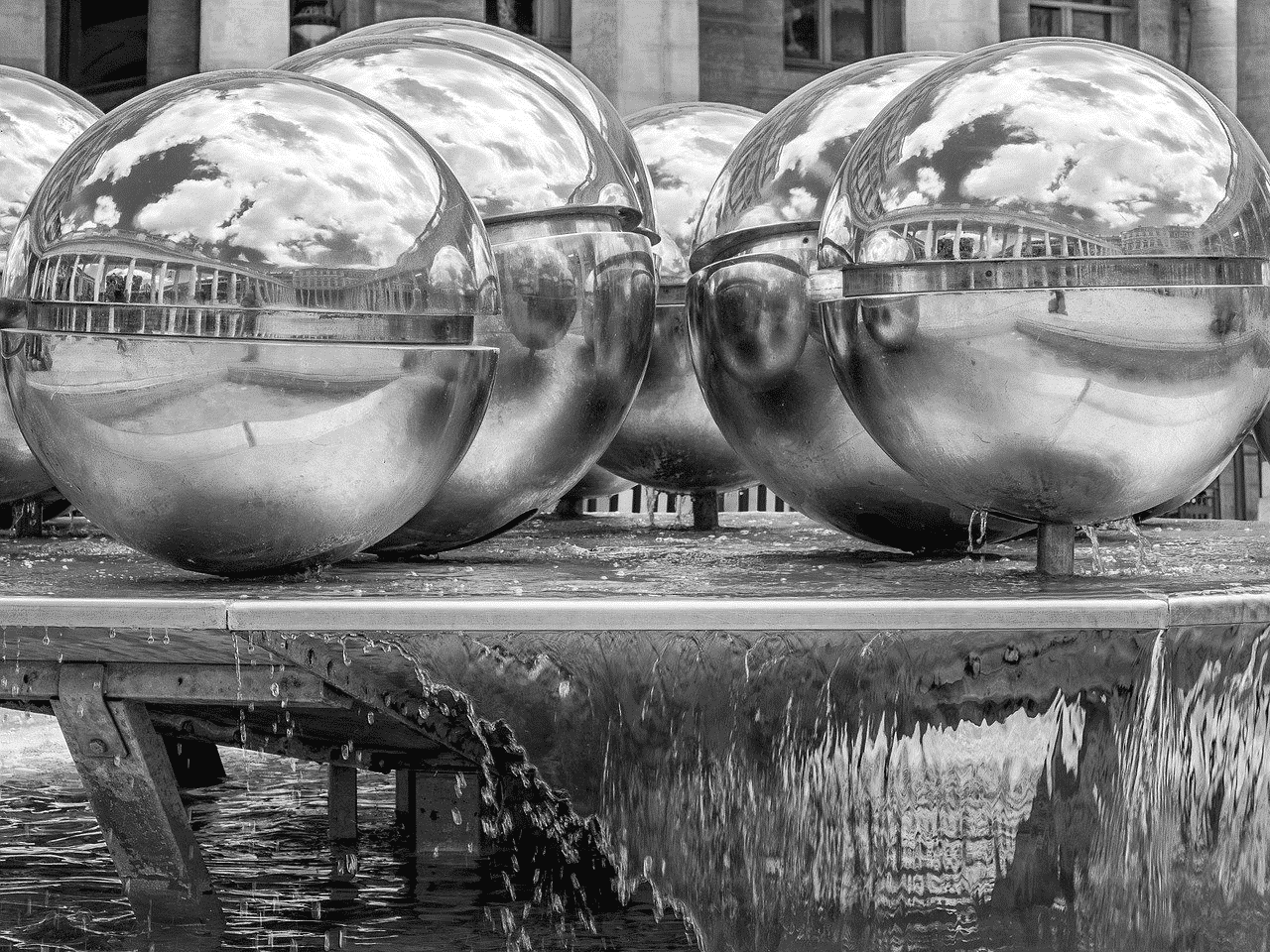
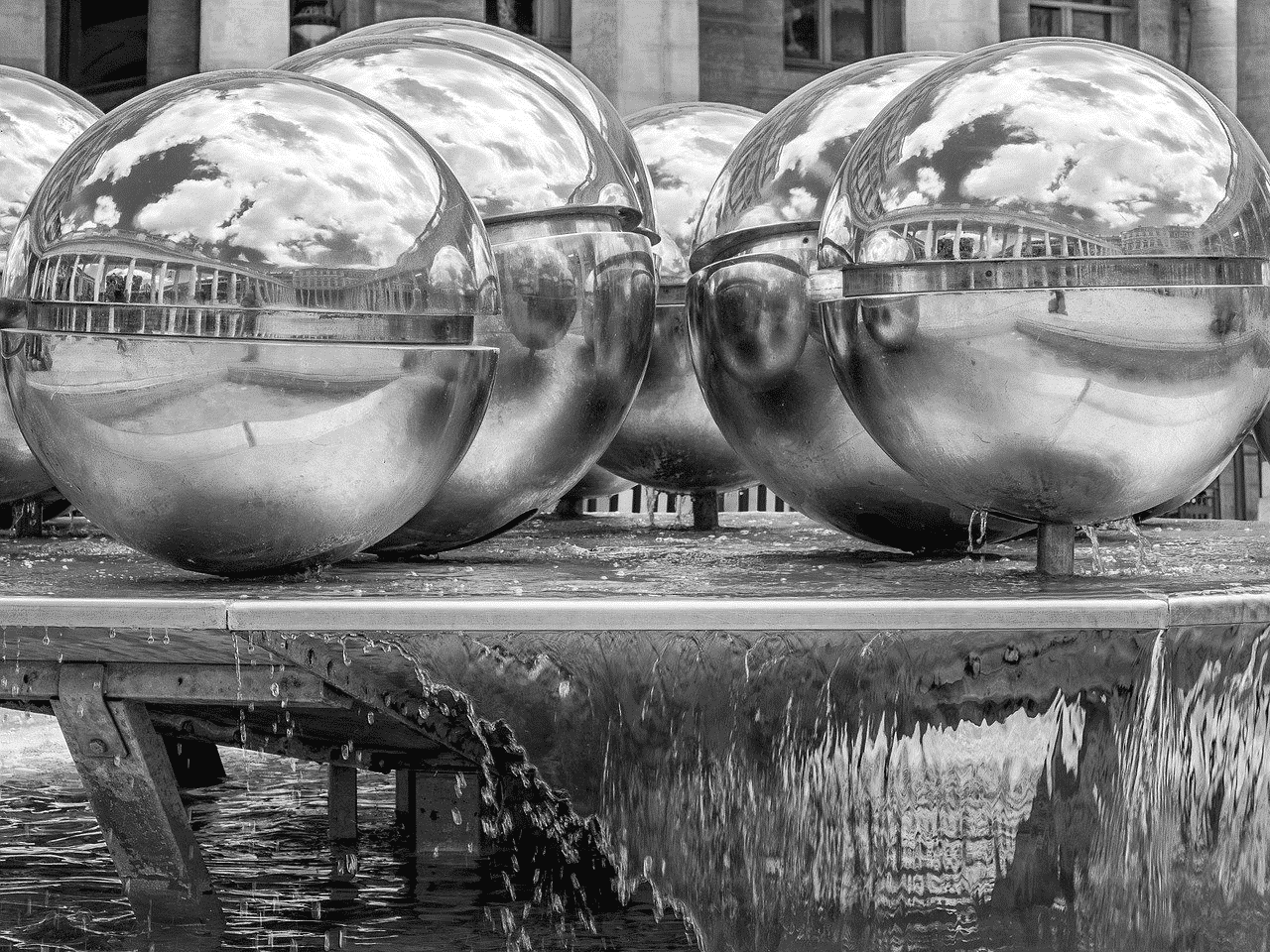

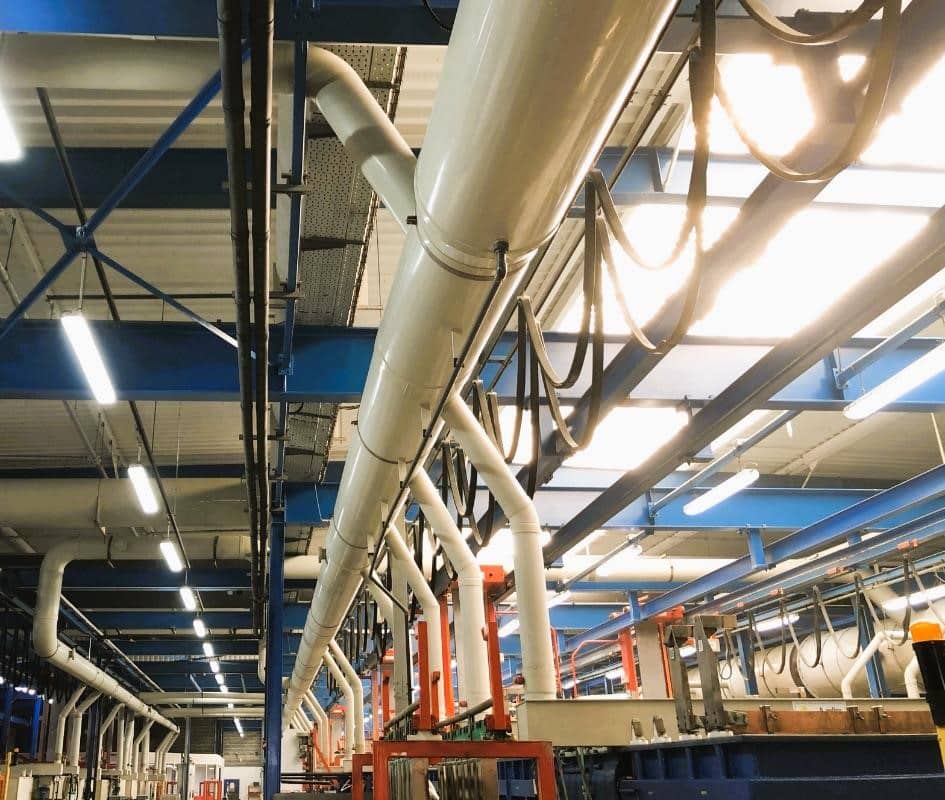
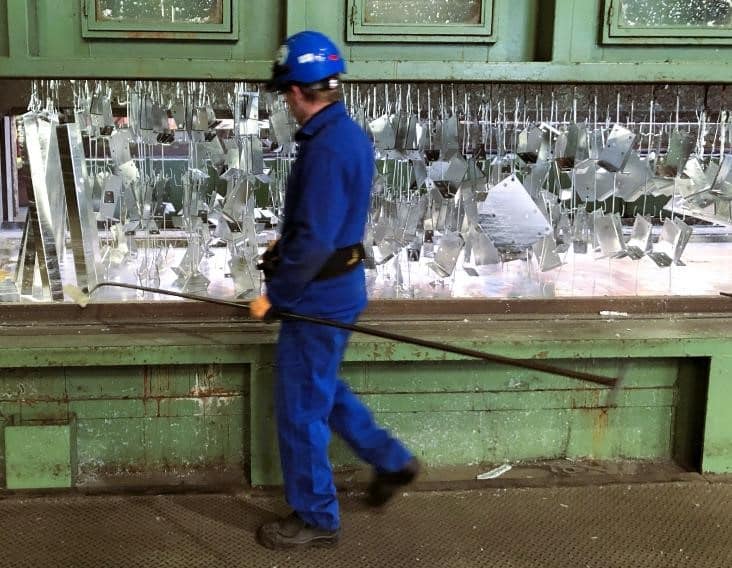